These fast-curing and high-performance
Isocyanate-Epoxy resins FPR
are two-shot
thermosetting systems based on liquid aromatic
polyisocyanates of the MDI family (component A) + liquid, di- or
multifunctional, glycidylether-type epoxies (component B).
Upon mixing of the two components A + B in a 70:30 or 60:40
weight ratio, the resulting
resins are odorless, low-viscosity liquids, with a pot-life at room
temperature adjustable
from 15 minutes to 6 hours. The subsequent polymerization converts them into hard
and high-softening materials, with a mixed isocyanurate-oxazolidone
chemical structure.
Through
their own specialty & proprietary polymerization catalysts FPC, the resin hardening time at temperatures
from 25 to100° C may easily be varied at will within a broad interval from
hours to a few minutes, and optionally made as short as 20-30 seconds at 80-100° C.
After
appropriate post-curing, the solid products are turned into densely
crosslinked and absolutely insoluble, amber-colored polymeric glasses, with a softening
point optionally as high as 320°C.
By varying the catalyst
type and concentration, hardening times can be
adjusted to fulfil the wide range of processing requirements including those of
the fast R-RIM, S-RIM, RTM, HS-RTM, and pultrusion
technologies, to those of the relatively slow Bag Molding, Liquid Injection
Molding, Vacuum Infusion Molding, and
resin casting techniques.
These
hard, moderate-cost thermosets are
further characterized by: 1) a superior hydrolytic, solvent and chemical
resistance; 2) an intrinsic flame resistance; 3) outstanding adhesion
to mineral glasses, ceramics and
metals. Besides the above characteristics, durability at
peak temperatures of 300°C, and at continuous service
temperatures of up to 200°C, make these resins materials of choice
as matrices for structural composites, for fabrication of parts and
components, embedding or
coating of electrical/electronic/electromechanical devices, and a variety of
applications whenever a critical combination of heavy-duty performance, fast processing and
competitive prices is a critical issue.
1.
Processability Characteristics
1.1
Pot-Life and Polymerization Rates
-
Pot-life
at temperatures up to 50°C:
perfect
latency (stability of the initial viscosity) adjustable from 10-15
minutes to 1-1.5 hours, depending on temperature, FPC
catalyst type and concentration.
-
Gelation times at
60-100°C:
from 20 seconds to 2 hours, depending on the catalyst
type & concentration.
-
Vitrification times at
60-100°C: from 40 seconds to 6 hours, depending on
the catalyst type & concentration.
-
The
resin hardening must be
completed by thermal after-treatments:
1
to 6 hours at temperatures from 150 to 240°C (typically, 1.5 ÷ 2
hours at 180 ÷ 240°C).
Plasticized FPR
resins
(with lower final Tg) require shorter post-curing
treatments, and/or lower post-curing temperatures (150 ÷ 180°C).
1.2
Microwave Processability
Thanks to the
peculiar physico-chemical properties and chemical mechanisms of action of
their specialty catalysts, these isocyanate-epoxy resins are
exceptionally-well suited to be cured and/or post-cured by microwave
heating. By means of such
processing techniques, the curing and/or post-curing times can typically be
reduced to 1/4 ÷ 1/10 of those required under conventional thermal conditions.
Novel
proprietary catalysts, specifically developed for the microwave processing
of FPR
resins (
FPC W1
e
FPC W2 ),
allow for the preparation of FPR
resin compositions endowed with the following, extremely
interesting combination of features: a prolonged pot-life at room
temperature (up to 4-6 hours), coupled with particularly short vitrification times under
microwave
irradiation, minimized to 1/8 - 1/10 of those under conventional
thermal treatments, at the same resin temperature.
1.3
Rheological Properties
-
Initial viscosity:
100 ÷ 600 cps
at 23°C, depending on the resin formulation, i.e. (without
any resin diluents) viscosity
values 5-10 times lower than those of known epoxy resin formulations,
and 2-4 times lower than those
of unsaturated polyester, and
conventional & multifunctional vinyl-ester resins.
2.
Properties of Cured Resins
2.1 Distortion Temperature
Glass
Transition Temperature ( Tg
~ HDT ). Depending
on the resin formulation: Tg of standard
Isocyanate-Epoxy FPR
S
resins = 250 ÷ 300 °C (typically: 270 ÷ 300°C); Tg
of specialty Isocyanate-Epoxy FPR
H
resins
= 300 ÷ 320 °C. Plasticized
formulations possess a glass transition temperature lowered to180 ÷ 240 °C;
for partially plasticized grades, the Tg spans the 230 ÷ 270°C range.
2.2
Thermal and Thermo-Oxidative Resistance
Fully cured
FPR
resins possess an
excellent thermal stability
up to 280°C, being currently able to sustain continuous use temperatures
> 150°C (typically,
of 160 ÷ 180, and up to 200°C),
and peak temperatures up to 350-360 °C. Their high-temperature aging, in
both inert atmosphere and air, implies a smooth and slow
weight loss, without any bulk and surface micro-structural damages (with the
resin surface remaining in fact smooth and brilliant). For
example, the weight loss of neat resin specimens is of 5 - 6 %
after 200 hours at 250°C in air; and that of glass
fiber-reinforced or mineral powder-filled resins (i.e., quartz-,
calcined clay-, silica-filled, etc.) [60 wt. % of fibers or mineral
powder] spans the 2.5 ÷
2.8 % interval after 2000 hours of continuous
exposure at 200° C in air.
2.3 Fire Resistance
Fully-cured, neat
FPR resins are inherently flame retardant (with respect to
neat unsaturated polyester,
vinyl-ester and conventional epoxy resins), and display a fire behavior not
so much different from that of phenolic and imide resins.
Classification according to
the UL 94 test method (Underwriters Laboratories), for 3.2 mm-thick
specimens:
-
neat
resins V1
-
resins
filled with common, inert mineral fillers (talcs, micas, clays)
V0
-
resins
filled with commercial, mineral flame retardants (10-20% by weight)
better than V0
-
partially
brominated resins
much
better than V0
2.4 Water Uptake and Chemical Resistance
-
In boiling water, as
well as in saturated moist air, the fully-cued resins display water uptake levels
remarkably below those exhibited by the best epoxy thermosets (maximum, equilibrium water
uptake capacities of FPR
thermosets = 0.9
÷ 1.0 % by weight).
Such values indicate a superiority of FPR
resins over
the entire category of epoxy materials, and particularly with respect to
the DDS-cured ones (with the highest Tg levels) for
structural, aerospace-grade applications (whose hydrophilicity problems,
hydration attitudes in moist air, and resulting remarkable rigidity
losses, dimensional instability issues, etc. are well recognized and
critically evaluated in the field of structural composite materials).
-
Thanks to the absence of hydrolytically- and chemically-weak
groupings (such as esters, amides and urethanes), as well as to the
perfect chemical neutrality of their specialty FPC
catalysts, the glass transition temperature and mechanical properties of
FPR
resins are
unaffected (or just minimally affected) by aging in both moist environments and
boiling water (even in the presence of surfactants). By virtue of their chemical structure, the resistance
to very aggressive chemicals is excellent as well. Only concentrated, strong
acids and bases can attack, and slowly degrade, the
surface of the fully-cured resins, which sustain indeed,
e.g., 12 hours in aqua regia at room
temperature, or 24 hours in boiling aqueous (20 wt. %) caustic
soda.
2.5 Mechanical Properties of
the Neat, Cured Resins
-
From the standpoint of flexural, tensile
and impact properties at room temperature, they are equivalent
to the best unsaturated polyester and vinyl-ester resins, as
well as to most conventional and specialty epoxy
thermosets:
flexural strength
at
23° C (ASTM D790) = 90 ÷
110
MPa;
flexural
modulus at 23° C ( ASTM D790) = 3 ÷
4 GPa.
-
As an important advantage over
the aforementioned reference resins, this level of mechanical properties is
well maintained over a broad interval from below room
temperature up to about 50°C below the glass
transition point of the particular isocyanate-epoxy
resin composition considered. Typically, in fact, flexural
modulus decays of only 20 ÷
25 % are shown over the
-50 ÷
200-220°C temperature range for the standard grade resins (FPR
S resins), and over the -50
÷ 260°C interval for the
high-Tg ones (FPR
H resins). Obviously, proportionally smaller stiffness
decreases are being displayed by glass or carbon
fiber-reinforced materials.
2.6 Mechanical Properties of Composites
Typical mechanical properties of
isocyanate-epoxy
structural composites (reinforcement: glass fiber woven
roving; overall fiber content: 70-75 % by weight, 55-59 %
by volume) are the following:
quasi-isotropic 8-ply
glass fiber-reinforced laminates (0, 90, ± 45°,
symmetrical); @ 23°C
flexural strength
|
ASTM
D790
|
500
÷ 550 MPa |
flexural modulus
|
"
|
19
÷ 21 GPa |
tensile strength
|
ASTM
D638
|
300
÷ 350 MPa |
compression strength
|
ASTM
D695
|
300
÷ 350 MPa |
orthotropic 8-ply
glass fiber-reinforced laminates (0, 90°); @ 23°C
flexural strength
|
ASTM
D790
|
600
÷ 650 MPa
|
flexural modulus
|
"
|
21
÷ 24 GP
|
The
excellent mechanical properties of fiber-reinforced FPR
thermosets are linked primarily to the high adhesion
of such resins to reinforcing fibers, as evidenced by the SEM micrographs below,
showing the fracture morphology of a glass fiber-reinforced FPR resin.
These micrographs exemplify the post-impact permanence of significant portions of the glassy
polymeric matrix firmly linked to the fiber surfaces, despite the
micro-morphology proper to a brittle fracturing of the composite. Such strong
FPR
resin-fiber adhesion is further demonstrated by the values of the
interlaminar shear strength (short-beam
shear strength, according to ASTM D2344) of glass and carbon
fiber-reinforced FPR
resin orthotropic laminates (at 23°C):
laminate
type |
short-beam
shear strength
|
glass fiber-reinforced
orthotropic laminates
|
55 MPa |
carbon
fiber-reinforced
orthotropic laminates
|
65 ÷ 70 MPa |
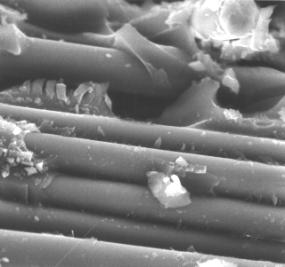
|
|
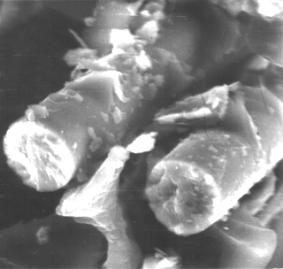
|
|
Fracture
morphology after a destructive
ball-drop
impact at room temperature of an RTM composite with an
ISOCYANURATE-OXAZOLIDONE matrix from the std.
FPR
S-1
resin, with a glass fiber (woven-roving) reinforcement. SEM
micrographs. |
-
Post-impact
mechanical properties:
as compared to commercial,
aerospace-grade carbon fiber/epoxy composites, evaluations of the residual mechanical
strength (tensile, flexural, and impact strength) of structural,
carbon fiber-reinforced FPR
laminates after
non-destructive ball-drop impacts allowed for rating them as
aerospace-grade materials, with the advantage of a 60-80°C-higher
distortion temperature.
2.7 Electrical Properties
These resins are
per se characterized by a
spectrum of electrical properties (i.e., dielectric
strength, dielectric constant and loss factor, surface and
volume resistivity, as well as thermal endurance) similar to
that of the best epoxy materials qualified on the market for
heavy-duty, low and medium-voltage electrical applications
(high-power electrical transformers, big capacitors and insulators, etc.).
Cast
thermosets from quartz powder-filled (60 wt.
%) FPR H-0
and H1
resins exhibit the following, typical properties:
dielectric
constant [25°C, 50 Hz]
|
IEC
60250
|
2.9
÷ 3.3
|
dielectric
loss factor (tan d)
[25°C, 50 Hz]
|
"
|
0.010
÷ 0.015
|
dielectric
strength (specimen thickness = 1 mm)
|
IEC
60243
|
28
÷ 32 kV/mm
|
dielectric
strength (specimen thickness = 2 mm)
|
"
|
18
÷ 22 kV/mm
|
Permanent
Service Temperature
|
IEC
60216
|
160
÷ 180 °C
|
Thermal
Class rating
|
IEC
60085
|
>
F class
|
3.
Main Grades of Isocyanate-Epoxy FPR
Resin
Systems Developed
3.1
FPR
Resin Systems
-
Resin System FPR S-1 :
Standard resin, with medium
viscosity and medium thermal-mechanical properties (HDT > 250°C),
flame resistance = V1 according to UL 94, transparent, pale amber color. General
purpose, high-temperature resin, and for manufacturing of composite
materials with glass, carbon and/or Kevlar® fiber reinforcements of
standard type.
-
Resin System FPR S-1
FG (food-grade): Novel,
food-grade,
fast-curing and standard-performance resin, with medium
viscosity and medium thermal-mechanical properties (HDT > 250°C),
flame resistance = V1 according to UL 94, transparent, pale amber color.
High-temperature and strongly chemically-resistant resin for items in
contact with foods and beverages; this resin system implies the use
of the special, food-grade Catalyst
FPC FG-2.
-
Resin System FPR S-2
(experimental grade):
Standard resin, with medium
viscosity and medium thermal-mechanical properties (HDT > 250°C),
halogen-free flame-retardant (V0 according to UL 94), translucent,
pale amber color. Resin for standard high-temperature composite
materials; high-temperature resin for general purposes requiring
halogen-free flame retardancy.
-
Resin System FPR S-3 :
Standard resin, with medium
viscosity and medium thermal-mechanical properties (HDT = 240-250°C),
partially brominated flame-retardant (V0 according to UL 94),
transparent, amber color. High-temperature resin for
standard composite materials, and general purposes, implying high
flame retardancy requirements.
-
Resin System FPR S-1 LV :
Very low-viscosity resin, with
medium thermal-mechanical properties (HDT = 220° C),
flame resistance = V1
according to UL 94, transparent, pale amber color.
High-temperature resin ideal fo manufacturing of composite materials
containing particularly high volume fractions of reinforcing fibers,
and especially for structural composites with very high mechanical
properties made by infiltration of densely packed preforms of glass,
carbon and/or Kevlar® fibers.
-
Resin System
FPR S-3 LV :
Resin similar to
FPR
S-1
LV, partially brominated flame-retardant (V0 according
to UL 94).
-
Resin
System
FPR H-0 : Very high-performance,
specialty resin, of dark brown color, with medium/high viscosity and
outstanding thermal-mechanical and chemical properties (HDT = 300° C),
flame resistance = V1-V0 according to UL 94. Resin for highly-demanding,
heavy-duty applications (high-temperature, structural composites
complying with aerospace standards; high-voltage electrical
applications; parts, components and protective coatings for
chemically and biologically strongly aggressive environments).
-
Resin System FPR H-1
: High-performance, specialty
resin, similar to FPR
H-0,
of amber color, with medium viscosity and high thermal-mechanical and
chemical properties (HDT = 280° C),
flame resistance = V1-V0 according to UL 94.
-
Resin System FPR
H-2 (experimental grade):
High-performance, specialty
resin, similar to FPR
H-1,
with relatively-high viscosity, halogen-free flame-retardant
(V0 according to UL 94).
-
Resin System FPR H-3
: High-performance,
specialty resin, similar to FPR
H-1,
with medium viscosity, partially brominated flame-retardant (V0 according to UL 94).
3.2
FPC
Curing Catalysts
-
Catalyst
FPC 1A :
"Pure
catalyst". Standard, medium/fast-curing
catalyst, for the standard
FPR S Resin
Systems . Clear, white to pale-straw oily liquid;
promptly soluble in resins at room temperature. Low-cost, dual-function catalyst:
fast-hardening catalyst + fast wetting and impregnation promoter for
reinforcing fibers in
composites. Best suited for RTM and LIM manufacturing of
highly qualified commodity and structural composites for automotive,
appliances and general construction uses.
-
Catalyst
FPC 1B :
"Pure
catalyst". Standard, fast-curing
catalyst, for the standard
FPR S Resin
Systems. Clear, pale-straw oily liquid;
promptly soluble in resins at room temperature. Convenient,
dual-function catalyst: rapid-hardening catalyst + fast wetting and impregnation promoter
for reinforcing fibers in
composites. Ideal for R-RIM, S-RIM, RTM & HS-RTM, LIM, as
well as pultrusion, manufacturing of structural composites for
automotive, appliances and general construction uses.
-
Catalyst
FPC 2A : "Pure
catalyst". Very fast-curing catalyst,
designed for the high-performance
FPR H Resin
Systems . Very
fast-curing
or low-dosage catalyst for the standard,
FPR S Resin Systems.
Clear, refractive,
honey-like, yellowish liquid; readily soluble in resins at room temperature.
For applications requiring thermosets with a superior thermal and
chemical performance level: recommended for high
continuous-service temperatures, uses in strongly oxidizing and/or
chemically aggressive environments, implying stressing wet/dry and/or
warm/cold cycles, etc. Well suitable for heavy-duty
electrical insulation purposes.
-
Catalyst FPC
CP-2A :
"Catalyst
concentrate". Masterbatch solution of the fast-curing
catalyst FPC 2A in a liquid mixture of epoxy resins. Clear,
pale-yellow, honey-like liquid; easily miscible with resins at room temperature.
Especially designed for a precise dosage of
FPC 2A catalyst in small-scale or occasional
manufacturing operations.
-
Catalyst
FPC FG-2 :
"Pure
catalyst". Special, food-grade
fast-curing
catalyst, especially designed for the food-grade
Resin System
FPR S-1
FG. Clear, yellow,
honey-like liquid.
-
Catalyst
FPC 2B :
"Pure
catalyst". Superfast-curing catalyst,
designed for the high-performance FPR H Resin
Systems . Ultrafast-curing
or very low-dosage catalyst for the standard FPR S
Resin Systems . Clear, refractive, yellow,
honey-like liquid; easily soluble in resins at room temperature.
For applications requiring thermosets with a premium thermal, chemical
and dielectric performance spectrum: ideal for high-temperature
structural composites for heavy-duty automotive parts, industrial
constructions and appliances, aerospace-grade composites, high
dielectric strength electric insulators for
high-voltage/high-temperature uses, etc.
-
Catalyst FPC
CP-2B :
"Catalyst
concentrate". Masterbatch solution of the superfast-curing catalyst FPC
2B in a liquid mixture of epoxy resins. Clear,
yellowish, honey-like liquid; easily miscible with resins at room temperature.
Especially designed for a precise dosage of the FPC 2B catalyst in small-scale or occasional
manufacturing operations.
-
Catalyst
FPC XF :
NEW! "Pure
catalyst". Ultrafast-curing catalyst,
for all the FPR H and
FPR S
Resin Systems
. Pale
yellow, low-melting crystalline solid. Designed to minimize (i.e.
further decrease the already low) concentration of the
FPC 2B
catalyst.
-
Catalyst FPC W1
:
"Pure
catalyst". Specialty,
fast
microwave-curing
catalyst for all the Resin
Systems
FPR S & H . It enables a long pot-life and
short curing and post-curing times under microwave irradiation.
Honey-like, light amber, refractive liquid; promptly
soluble in gently warmed resins. It imparts to isocyanate-epoxy
thermosets the same high-performance spectrum provided by Catalyst
FPC 2A.
-
Catalyst FPC
W2
: "Pure
catalyst". Specialty,
superfast
microwave-curing
catalyst for all the Resin
Systems
FPR S & H. It ensures a long pot-life and particularly
short curing and post-curing times under microwave irradiation.
High-viscosity, amber-colored, refractive liquid; easily
miscible in gently warmed resins. It provides isocyanate-epoxy
thermosets with the same premium performance spectrum enabled by Catalyst
FPC 2B.
|